Frozen lines. Cracked pipes. Slow starting compressors. Or worse, compressors that won’t start at all. Winter can be difficult on compressed air systems—even here in the South. Most air compressor equipment should be kept above 40º F to maintain efficient operation and avoid costly breakdowns. As we enter the coldest months of the year, it’s important to winterize your system and know what maintenance needs to be performed throughout the winter season to protect your investment.
How to Get Your Equipment Ready for Winter
- Ensure weather stripping is in good condition.
Inspect all weather stripping and replace any areas where it is showing signs of wear and tear or not working properly. - Check condensate drains throughout the system.
Condensate drains help remove water from your compressed air system. If they are damaged or obstructed during cold weather, moisture can freeze, which may lead to clogged pipes or other compressor malfunctions. - Inspect insulated areas for leaking heat.
For air compressor parts that are exposed to the elements, proper insulation is essential to keep heat inside and cold outside. Install heat trace tape on any exposed parts. - Check air intake openings.
Inspect the air compressor intake regularly during winter use. If the intake is exposed to wintery conditions, it can easily be damaged by snow, rain and ice. - Protect compressed air receivers.
Condensate that collects at the bottom of a receiver tank can freeze and cause system issues. Insulate all outside pipes feeding the tank as well as the condensate drain for the tank and ensure the drain is working properly. - Replace old air dryer and compressed air filters.
Like drains, filters work to remove condensate from your compressed air system so it can’t freeze. Performing regular maintenance and replacing old and damaged filters is critical if you’re using a compressed air system in cold temperatures. - Protect outdoor equipment with external heat sources.
If your compressed air equipment must be kept outside during cold weather, take efforts to shield it from the wind and use floodlights or heat lamps to keep controls from freezing.
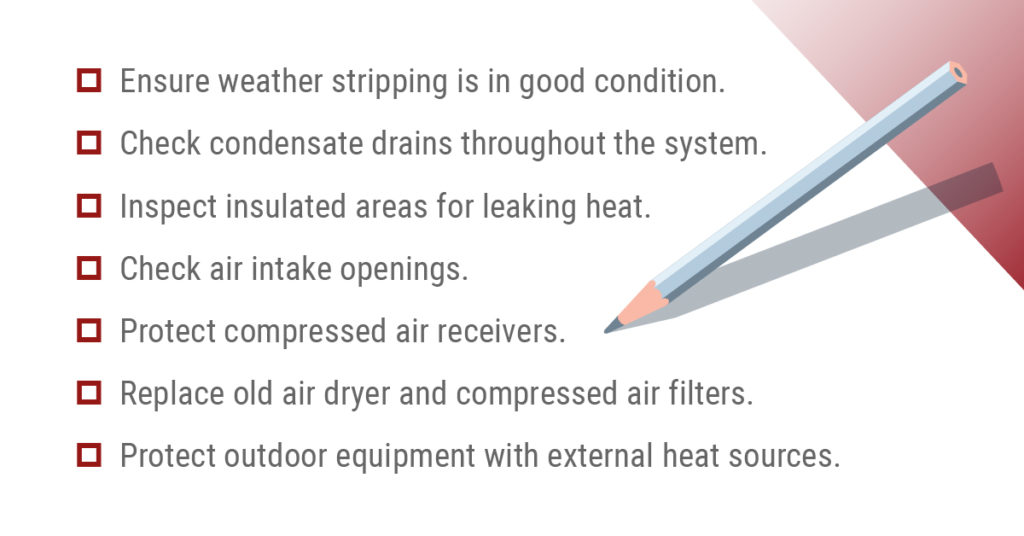
Need help winterizing your system? Has it been a while since your equipment has been serviced? Or is your air compressor not working as well as you would like? Our experienced service team can help you address any cold weather vulnerabilities you may have. Contact Lewis Systems or call 800.222.4553 to discuss your compressed air needs and how we can help you keep your operation performing at its best all year long.